6 June 2010
Risk Assessments
The Management of Health & Safety at Work Regulations 1999 tells us that we must conduct risk assessments so that the hazards in the workplace can be identified, then assessed so that control measures can be identified and put in place to reduce the risk of injury to employees, visitors and contractors.
The HSE are currently focussing on risk assessments in the workplace, but particularly looking at machine risk assessments following the recent fatalities and serious injuries in the printing industry.
The definition of a hazard taken from the Management Regulations 1999 (ACOP): –
Something with the potential to cause harm (substances or machines, methods of work and other aspects of work organisation.
The definition of a risk taken from the Management Regulations 1999 (ACOP): –
The likelihood that the harm from a particular hazard is realised. The extent of the risk covers the number of people affected and the consequences for them. Therefore, risk reflects both the likelihood and severity of the harm.
Risk assessing is not an office bound exercise and must be evaluated where the operation happens and when possible, involve the persons who actually do the job or operate a particular piece of equipment.
You must record what the process is and who is at risk. Think who could be at risk directly but make a note of those who could be affected indirectly. How long will those persons be exposed to the hazard i.e. hourly, daily, weekly, monthly, etc.
Record what the hazards are and what control measures are already in place, such as guarding, pre-use checks, maintenance schedules and employee training, this list is not exhaustive but will give you a feel for what is required.
From this information you can now work out what is the residual risk level and what needs to be done to further reduce the risk.
Residual risk is measured by the severity x likelihood.
Once you have got your residual risk level you will need to put some control measures in place to reduce the risk further.
Implement regular documented checks by the operators.
If possible, eliminate the cause of the danger; for example, could the machine be replaced with new equipment? In the case of noise, for example, on stitching lines can the compressor(s) be located outside of the building in a sound proofed box?
Reduce the need for people to approach the dangerous parts of the machine, this can be as simple as re-locating a walkway.
Access to dangerous parts of a machine needs to be made as difficult as possible by fitting fixed or interlocked guards.
Personal protective equipment (PPE) should always be a last resort and never the first thing you think of.
Train your employees to improve their recognition of danger areas and what can be done to avoid them.
Safe systems of work must be in place giving the employee a set of rules to follow to reduce the risk of injury.
Signage must be in place warning people of possible hazard areas, such as hot surfaces, and that the machine must be stopped and locked out before removing any panels, etc.
The mechanical hazards are slips and trips, impact injuries, contact with moving parts, entanglement, and the failure of components (bearings, etc).
Non-machinery hazards can be electrical failure, exposure to chemicals, temperature, noise, vibration and human intervention.
Some of the machinery hazards in printing are transmission machinery, conveyors, ink rollers, gears, nipping rollers and printing cylinders.
Just because you haven’t had an accident on a particular machine or process, don’t ever assume that the machine or process is safe.
Intergraf Economic News (Paper Prices) - March 2024
18 March 2024
Access the latest edition of the Economic Newsletter for the European Printing Industry for data on paper consumption, and pricing data for pulp, paper and recovered paper. Data for packaging papers and board is also available with this edition.
STUDY EXPOSES HIGH COST OF PHARMACIES PRINTING MEDICAL INFORMATION LEAFLETS
7 March 2024
Intergraf welcomes the release of a study by our partner MLPS (Medical Leaflet = Patient Safety), a subgroup of the European Carton Manufacturers Association (ECMA) shedding light on the potential economic costs associated with the proposed use of Print on Demand (PoD) leaflets in the pharmaceutical legislation revision.
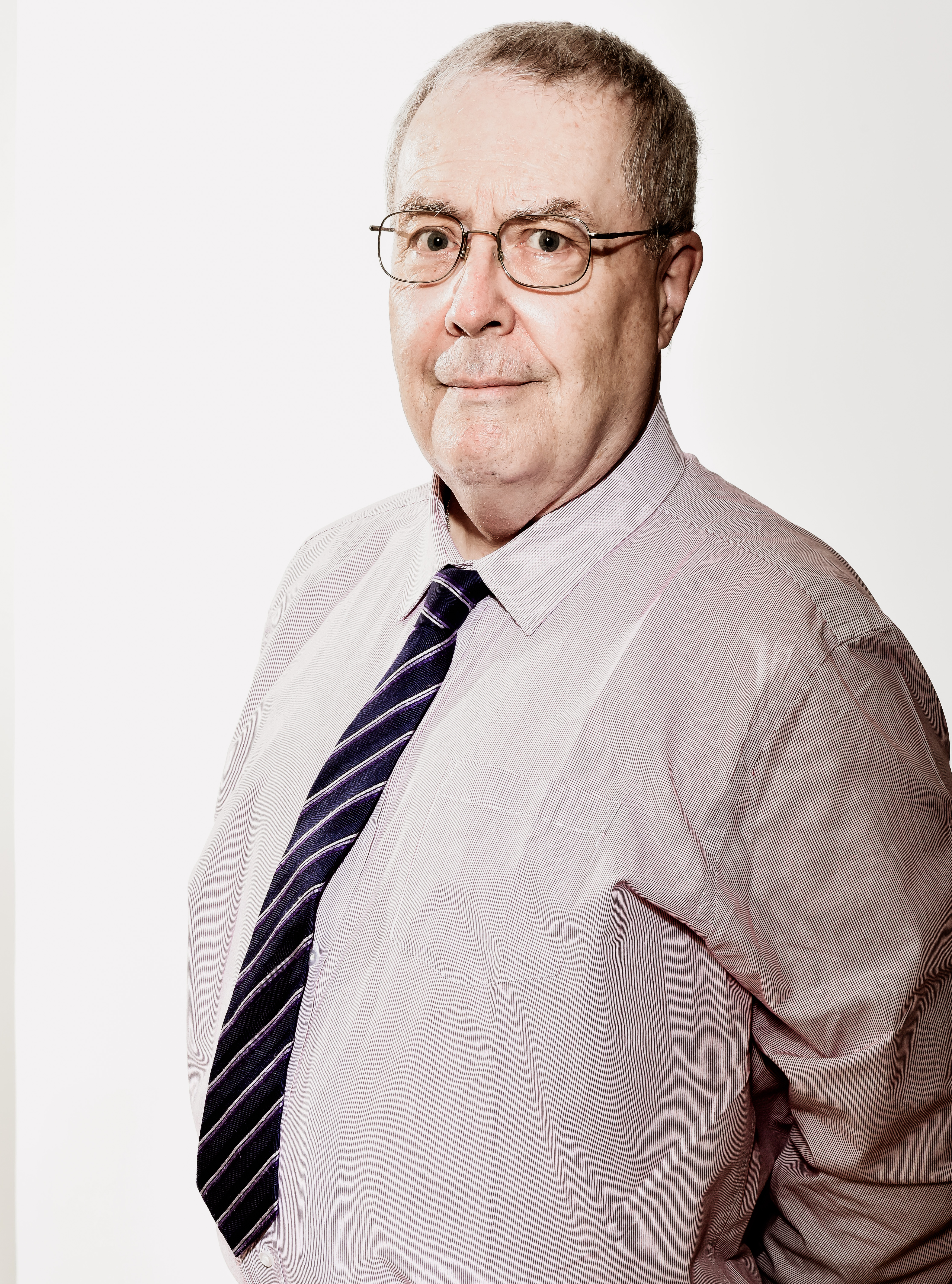
The BPIF is the printing industries champion. By becoming a member you join a diverse and influential community. We help you solve business problems, connect you to new customers and suppliers and make your voice heard in government.
Call 01676 526030